When stiffening ductwork or other sheet metal products, there are two primary techniques fabricators can employ, cross-braking or beading. Before we get into the specifics of how and when to perform each technique, let’s take a step back and ask the question, “Why should I stiffen my sheet, anyway?”
The primary reason for taking production time to stiffen and strengthen duct is compliance. SMACNA sheet metal standards deem that ductwork of various gauges should be put through a stiffening process, and with good reason. Since we’re talking about constant or near-constant air flow through these parts, the material needs to be durable enough to handle the pressure and temperature changes. A duct that lacks the strength provided by stiffening can warp, leading to impaired air flow or rattling and banging noises during operation.
There are a few methods to stiffening duct, and choosing the ideal method depends on the context of your situation. One consideration fabricators must make is whether they are working with a round or oval duct, or a rectangular duct. Round ducts are strengthened by implementing stiffening ribs at equal intervals, which is altogether another process than we’ll be covering in this blog. Cross-braking and beading are both techniques that are used with rectangular duct. Your volume goals and the machinery available at your workshop will help you determine which stiffening method you should use.
Cross-braking is a technique performed using a press brake. To form, the operator marks the bend line on the sheet as a guide, then lines it up with punch tip and performs a shallow bend. A second bend is made across this initial one, leaving an “X” impression on the sheet.
Beading strengthens duct in a similar fashion in that it leaves an impression in the sheet, but these impressions will not intersect like they do in cross-braking. The process also must be performed using a beader machine, which is fitted with specialized tooling specifically for stiffening processes. Roto-Die produces a SMACNA beader with a capacity for 16-30 gauge mild steel up to 5’ wide, with 5 beads of adjustable depth.
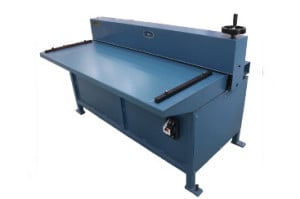
Lockformer Beader, SMACNA Bead Pattern
So What Should You Use?
The deciding factor between these two techniques will come down to a workshop’s volume goals. Press brakes and benders are suitable for a diverse range of applications, like box forming, channel forming, and hemming. It is therefore a good practice to have this machine free from stiffening operations, especially in environments with higher output goals. In these cases, having a beader on site that can stiffen simultaneously alongside the otherwise occupied bender can maximize the output of final parts per shift.
What stiffening operation does your shop prefer to use? Comment below and tell us: are you a “Beader,” or a “Cross-braker?”