The following blog post is part two of a multi-part series in which Mestek Machinery discusses the importance of a good shop layout and the ways in which our customers can improve their shops’ productivity by creating an efficient environment for production.
Next Steps
Now that you have learned the basics of proper shop layout, you may be asking yourself – what are the steps I need to take to make my shop more efficient? To answer that, you can take yourself on a shop inspection tour and ask yourself a couple of simple questions:
- Is there any wasted movement that we can avoid?
- Is there anything that we can do to remove a hazard or to improve safety?
- Is there any unused space that we can put to good use?
- Is there anything that we do not use that we could get rid of?
The Principles of Shop Layout
When a sheet metal contractor is setting up a shop, there are 6 basic principles to setting up a better shop:
1.) Work Flow
A good shop layout makes use of a work area arranged so that the pieces running through it are made in a linear sequence.
2.) Minimum Distance
Materials should always move the minimum distance possible between operations.
3.) Satisfaction & Safety of Employees
Employees should not be secondary a company’s product. Happy employees = productive employees.
4.) Space Available
Properly using all of the space available in a facility is key to getting the most out of a property. Overhead space is often wasted or used improperly.
5.) Flexibility
A proper shop layout takes into account the future use of the space a shop has to work with. If a shop needs to make minor adjustments, is it set up so that rearrangements can be made at a minimum cost?
6.) Overall Integration
Merging the first five principles of shop layout is vital to implementing an efficient shop layout into a sheet metal facility.
Analyze you Shop Operations
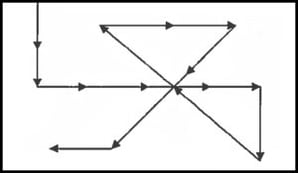
Incorrect Flow Shop Layout Diagram
When taking your shop inspection tour, you should analyze each of the following operations:
- Receiving
- Storage of raw materials
- Shearing
- Layout
- Cutting and notching
- Punching and Drilling
- Insulating or Lining
- Assembly
- Shipping
Continuous Flow Line
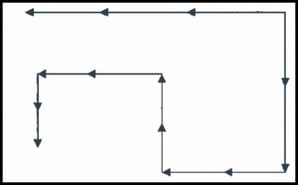
Continuous Flow Shop Layout Diagram
If one were to visit every sheet metal shop in the country and compile a list of the best shops, the best of them would all have at least one thing in common: they all have a continuous flow of materials. This means that all materials used in the shop flow through the various operations in a shop from receiving the raw materials to shipping the finished product without any interruption. If materials in a shop pass back and forth between employees and the paths from each operation cross one another, then the layout is likely highly inefficient and disorganized. A continuous flow provides the following advantages:
- Increased production
- Reduced fatigue
- Minimized floor space required of square feet
- Reduced storage areas